• Trusted & Verified
• Through our vendor managed program, we carefully research and prequalify our vendors to ensure product is procured from safe and reputable sources. In addition, we thoroughly prescreen all prospective vendors based on a rigorous set of product quality, dependability, and service standards.
• Once a supplier is added to the Yufo “approved vendor list,” we continually monitor and grade each supplier based upon a set criteria, including product quality history, performance and service fulfillment – identifying any potential problems or concerns well in advance, before product ever reaches our customers.
Rigorous Quality Inspection Process 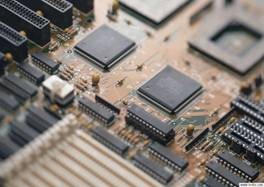
• Level 1: Visual Inspection
• Visual inspection and authenticity verification is conducted on all incoming materials by Yufo inspectors. Visual inspection review includes:
• 1、Manufacturer P/N, quantity, and date code verification
• 2、Body marking inspection (faded marking, broken text, double print, ink stamps, etc.)
• 3、Physical conditions inspection (lead bend, scratches, chipped edges, etc.)
• 4、Taping condition inspection (dented packet, missing parts, etc.)
• 5、Verify moisture barrier protection verification (vacuum sealed, humidity indicator with specification)
• 6、Original factory sealed components vs. non-factory seal
• 7、Any visual irregularities
• Level 2: Engineering Review
• Materials identified as questionable during the visual inspection process are reevaluated by Yufo staff engineers. Product sampling plans are also employed to ensure product consistency. Engineering review includes:
• Review of level 1 findings
• 1、Counterfeit databases referenced and updated
• 2、Label verification (bar code and label review)
• 3、Manufacturer logo and date log verification
• 4、ERAI counterfeit alert program
• Level 3: Testing
• Product testing is completed to ensure that any questionable materials meet manufacturers" specifications. Product samples are also periodically tested to ensure product consistency and testing. Testing includes:
• 1、Decapsulation test
• 2、Solderability test
• 3、Surface contamination analysis
Electronic Components Distribution - Testing
• To ensure the broadest, deepest and most dependable network of quality electronic components, Yufo has developed a global network of third-party testing laboratories to provide expert product testing during quality assurance evaluations.
•
• Testing of products is completed by certified partner laboratories that work to ensure that materials identified as questionable meet manufacturers’ specifications and requirements. This global network provides Yufo access to technical know-how and state-of-the-art technology, adding these core competencies to our distribution service offerings.
• In addition, electronic component product samples are randomly selected and tested periodically to ensure product consistency and vendor quality and confirm internal quality controls.
• Testing conducted includes:
– Decapsulation
– Solderability
– X-ray examination
– Contamination analysis
– DC & AC functionality
– Calibration and capacitance measurement
– Electrical